Compliance & Technical Folder Management
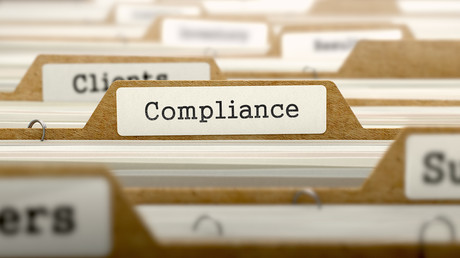
If you are just beginning or have been supplying products onto the Australian and New Zealand markets for a while, compliance can often be a confusing and time-consuming proposition. It is also extremely important to understand your ongoing legal obligations.
At Comtest we have been assisting local and international clients to get their products to market and ensure they meet their initial and ongoing compliance obligations for compliance in Australia and New Zealand for over 20 years. Comtest Group offers a comprehensive range of testing, certification, consulting and compliance documentation services, both in-house and through our network of partners around the world.
Clients looking to bring products such as telecommunications and electrical products onto the Australian and New Zealand markets are assisted right through the process, from testing, assessment and gap analysis of existing test reports, certification, registration, documentation storage and maintenance. If you are looking to access the world markets, we can offer a full range of services working with our fully accredited third-party test and service providers.
When supplying any electrical or electronic products that operate using any voltage onto the Australian and New Zealand markets, there are many requirements that need to be considered. One such requirement is the keeping of records, and compliance documentation.
Comtest’s Compliance Folder Management Pty Ltd (CFM) is the expert when it comes to assisting our clients with all their ongoing documentation and compliance obligations.
CFM has been assisting both local and international clients to meet compliance requirements for over 20 years. CFM works closely with clients to audit, store and maintain their documentation to comply with ongoing compliance and record keeping, in line with:
- the ACMA regulatory framework for all electronic products;
- the Electrical Equipment Safety System (Electrical Regulations); and
- ACCC recommendations.
We can assist with your legal obligations for new or existing products that are to be supplied onto the Australian and New Zealand markets by:
- reviewing and conducting a gap analysis of test reports and associated documentation;
- acting as an Agent for international suppliers;
- registering products on ERAC’s EESS database;
- organising any additional testing in-house or through an appropriate partner test laboratory;
- applying on behalf of the client for Certificates of Conformity and Suitability from an Accredited Certifier;
- storing compliance folders;
- managing compliance and technical folders by monitoring time frames and confirming with clients any changes that may need to be made to the compliance or technical folders in order to remain up to date and/or compliant;
- assisting and/or managing product recall processes and requirements — working with the client and government agencies to minimise any potential impact.
The ACMA regulatory framework for products supplied to the Australian market includes regulatory arrangements covering:
- telecommunications customer equipment and customer cabling;
- radiocommunications devices;
- electromagnetic compatibility (EMC) performance of electrical and electronic devices, vehicles and devices with internal combustion engines;
- electromagnetic energy (EME) from radio transmitters.
Each of the four regulatory arrangements incorporates a legislative instrument, referred to as a labelling notice. The labelling notices identify the applicable technical standards and testing, record-keeping and labelling requirements for products supplied into Australia.
A supplier should consult the relevant labelling notice/s to identify the requirements that apply to each product that is being supplied in Australia. A supplier must ensure a product complies with all applicable requirements (legislative instrument) before supplying that product to the Australian market. Comtest has assisted thousands of clients with compliance in this area.
Certain low-risk products (including under EMC and radiocommunications regulatory arrangements) may not require testing to demonstrate compliance. However, even if a product is not required to be tested, a supplier should be confident that the product complies with the applicable ACMA Technical Standard before signing the supplier Declaration of Conformity. This may be evidenced by a manufacturer’s performance specification documents for the device.
However, for most products, testing and test reports are required to prove that a product complies with applicable ACMA technical standards.
The specific testing requirements are based on a risk assessment of the potential consequences arising from supplying a non-compliant product. The higher the compliance/risk level, the more stringent the requirements for evidence of compliance and for record-keeping.
Each regulatory arrangement includes record-keeping requirements for product compliance.
Record-keeping requirements apply to a supplier of a product to which a compliance label has been applied. Comtest has assisted thousands of clients with compliance in this area.
The Electrical Equipment Safety System
The Equipment Safety Rules outline the processes required to address the legislative requirements of the Electrical Equipment Safety System. They do this by providing a framework which defines the processes, and the roles and responsibilities of key parties.
The key elements of these Equipment Safety Rules are as follows:
a) All electrical equipment cannot be sold unless it is electrically safe, regardless of the voltage type or voltage.
b) All in-scope electrical equipment is classified into one of three levels based on risk assessment.
(In-scope equipment is defined as operating on or supplying voltages for 50V ac rms – 1000V ac rms and 120V dc Ripple free – 1500V dc Ripple free.)
c) All Responsible Suppliers of all in-scope electrical equipment offered for sale must be Australian or New Zealand legal entities (including foreign companies with an Australian or New Zealand business registration) and must be registered on the National Database as Responsible Suppliers.
d) All level 2 (medium risk) and level 3 (high risk) electrical equipment must be registered on the National Database before it is offered for sale.
e) Documentation and evidence appropriate to the level of risk must be prepared and kept by the Responsible Supplier.
For level 2 (medium risk) electrical equipment, a Compliance Folder is required and, if not held by the Responsible Supplier, must be made available if requested.
For level 3 (high risk) electrical equipment, a Certificate of Conformity (Approval) is required.
f) All in-scope electrical equipment must comply with relevant standards and be electrically safe.
g) Regulators and Accredited Certifiers are able to assess test reports and are able to issue Certificates of Conformity for electrical equipment.
h) Certificates may be issued for levels 1, 2 and level 3 equipment. Requirements for the issue of a certificate include Australian Standards or joint Australian and Standards New Zealand product Standards that apply specifically to the type, or a standard accepted by a Regulatory Authority as a standard that can be readily applied to the type.
Certificates for level 1 and 2 are issued on a voluntary basis (referred to as Certificate of Suitability) subject to meeting the same criteria as that required for level 3 equipment (referred to as Certificates of Conformity) as detailed in these Equipment Safety Rules.
All Certificates issued under the EESS must have the appropriate details registered on the National Database.
i) All Certificates to be used as evidence of compliance must have the appropriate details recorded on the National Database.
j) All in-scope electrical equipment must be marked with a Regulatory Compliance Mark (RCM).
k) Responsible Suppliers must make a declaration that all in-scope electrical equipment that they supply is electrically safe.
l) Failure by a Responsible Supplier to discharge their obligations under the EESS will result in the imposition of significant penalties and possible de-registration.
Comtest has assisted thousands of clients with compliance obligations in this area for over 20 years. If you would like to know more, please contact us on +61396455933 or visit our website: www.comtestgroup.com.
References:
www.acma.gov.au
www.erac.gov.au
www.productsafety.com.au
PanJit Semiconductor — A new line of discrete semiconductors at TME
Transfer Multisort Elektronik has announced that it is now a global distributor of the products...
RMIT research shows connection between internet access & stockmarket stability
An RMIT study into the 2010 withdrawal of Google from mainland China has examined the impact of...
Australian EdTech sector generates 2.9 billion in revenue
A report by EdTech acceleration company, EduGrowth, has found that the EdTech sector turns in a...