Traceability in torque measurement
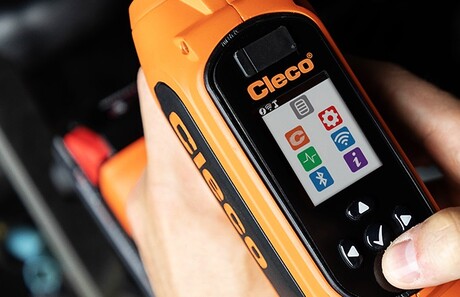
The traceability procedure of calibrating torque tools within assembly processes is crucial for obtaining accurate data records within the production process.
The manufacture of critical joints that occur in high-stress components places heavy demands on manufacturers, thus making screw-tightening a very important task in today’s assembly process. Industries such as aerospace, medicine, transport and electronics are utilising traceability for quality recording and statistical data that is used for ongoing processes and quality improvement, as well as meeting safety guidelines and quality control standards.
Importance of precise measurement
Precise measurement of torque requires each individual fastener and joint to be tightened precisely to the correct torque specification, which then needs to be individually checked, verified and recorded for traceability and quality purposes. In any kind of production process, not only the task should be properly designed but the measurement system should also be properly implemented. If the torque is not applied properly and the tension on the bolt torque is too low, varying loads will act upon the bolt and it will fail. The most important factor in a calibration process is decreasing its uncertainty and improving torque accuracy.
Intelligent transducerised assembly systems from Kolver
As challenging as this may all sound, fortunately there are many reliable screwdriving and screw feeding solutions on the market today. These are available in both handheld and fixtured configurations, which many industries use in situations where it is essential that all screws are tightened to the correct torque. At Hawker Richardson we strive to present a range of assembly tools that covers most of our customers’ fastening requirements. We recently sourced the Kolver range of electric screwdrivers to cover the increasing demands of the electronics and high-tech industries, where torque accuracy and traceability is very important. K-DUCER is the new class A intelligent transducerised assembly system. The system consists of an advanced state-of-the-art controller and a range of handheld and fixtured electric screwdrivers. Kolver K-DUCER electric tools cover all assembly line requirements for accurate, high-quality torque and angle-controlled tightening. The built-in compact transducer provides torque control with excellent repeatability.
The Kolver K-DUCER range covers:
- Unsurpassed ergonomics and soft touch design
- LED status Indicators (ok, error, tightening, etc)
- Temperature protection
- Full traceability and error proofing capabilities: 100% compatible with Industry 4.0
- Touch screen colour display
- Multiple programs and sequences
- Intuitive programming interface
- Precise torque and angle control
- Graphs output
- Perfect integration with Industry 4.0
Certificate of calibration traceable to a NATA certified instrument
Weber’s product range of screw feeding equipment offer solutions for various applications. Their transducerised torque and angle control products are used for processes where the tightening torque is safety critical. Transducerised systems have a precision internal torque transducer and angle encoder and can be supplied with a certificate of calibration traceable to a NATA certified instrument.
Cellcore
The introduction of Cleco Cellcore ‘Smart’ battery tools is the latest weapon in Hawker Richardson’s range of assembly tools with full error proofing and traceability.
This extremely versatile range of tools can handle torques from 0.5 to 2000 Nm with the advantage of being completely portable.
The tools can operate ‘standalone’ with an easy-to-program keypad interface on the tool and the ability to store the data of 15,000 rundowns. This makes them ideal for any off-site assembly requirements, particularly for solar and wind farms.
Traceability in torque measurement plays a critical and vital role in the assembly process, while ensuring tools are working as they should be, giving correct readings, providing a safe working environment for end users, and ensuring that companies are upholding their legal obligations.
Originally published here.
DC Microgrids: The next step in energy evolution
As we face environmental and energy challenges, DC microgrids can help pave the way for a...
Eliminate Unplanned Downtime: A Smarter Approach to Machine Diagnostics with the HYDAC HMG 4000
The HYDAC HMG 4000 portable data recorder provides a smarter, faster, and more precise approach...
Precision in Design: Specifying Large Handheld Enclosures for Industrial Electronics
When designing handheld electronics, ergonomics play a vital role; purpose-built plastic...