3D Power Packaging® for low-power DC/DC converters
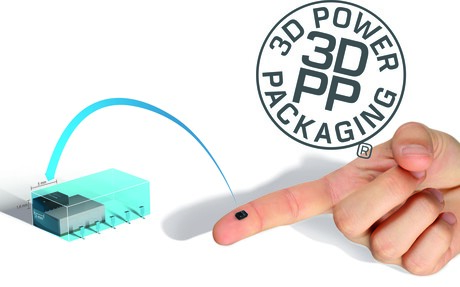
A long-term goal for RECOM has been to develop DC/DC converters which can be handled, placed and soldered like any other modern SMT component, but also with a low profile to match today’s slimline products.
What are the challenges with current packaging design for DC/DC converters?
Power density is one of the most important properties of a modern DC/DC converter design. Shrinking the design requires placing power components closer together. By doing so, you’re placing multiple heat sources near one another, so one of the main challenges current packaging designs face is getting the heat out efficiently. Thermal design considerations in very high density designs become crucial.
Another major challenge with any DC/DC converter design is EMC. One way to increase the power density is to shrink the size of the passives by increasing the operating frequency of the converter (faster switching requires smaller component values). But if you do this, the layout of the board often determines if the converter will pass or fail an EMI test. A good way to keep the parasitic elements in a circuit low is to limit the length of connectors on your PCB, but traditional packaging designs have limits to how short these traces can be.
What are the benefits of advanced packaging techniques?
One of the advanced assembly techniques which really helps to overcome the challenges of current packaging designs is FCOL (flip-chip-on-leadframe) power components. This technique not only significantly reduces the connection parasitics, but by flipping the IC and placing it directly on a leadframe, the FCOL design also has a dramatically reduced thermal resistance. The assembly technique allows higher switching frequencies to be reached while still meeting strict EMC requirements.
In RECOM’s 3D Power Packaging® technology, we additionally put active and passive components directly inside the PCB. This achieves similar results to the flip-chip-on-leadframe approach by shortening power paths and reducing the thermal resistance of the design, thereby allowing us to reduce the solution size and increase the performance of the module.
We’re also using different techniques to solve different problems. There is no point making the converter smaller if you can’t manage the heat and the electromagnetic disturbances it then creates. Customers often demand a holistic solution which addresses all thermal, EMC and power performance requirements in a single unit — in other words, they want a plug-and-play solution. For such customers, the RPM series is the way to go. It is a compact module that requires the minimum of external components (for example, two resistors to set the output voltage) to create a complete DC/DC power supply.
How is RECOM Advanced Packaging technology used for low-power DC/DC converters?
Advanced packaging technologies such as 3D Power Packaging are used in over-moulded flip-chip-on-leadframe designs, embedded active and passive components in the PCB, and multi-level designs. This helps RECOM to increase power density and raise switching speeds without harming the thermal performance.
Tell us about your products leveraging advanced packaging technologies.
The RPM, RPMB, RPMH and RBB series all use thermally optimized, multilayer PCB technologies with BGA chips and the RPX series incorporates FCOL technologies. And finally, the new RxxCTxxS uses a multi-level design and air-core transformer to reach very high isolation levels in a very low profile, IC-type over-moulded package.
The application of product is closely related to the development of industries. Can you share some applications that RECOM Advanced Packaging technology mainly focuses on?
We are very fortunate that our large product portfolio addresses various customer segments across the industry. The 3D Power Packaging products suit almost all kinds of applications and fulfil the market requirement of minimized PCB footprint, high power density, fully automated production process and time to market, as well as ease of use.
One example is drone applications (see image); the power module shown in the drone is up to 6 A for high power, which is good for the battery in drone applications. Other uses include telecom applications, ie, set-top boxes and gateways, for smart metering like 5G, industrial, robots, medical, mobility, energy, automotive, etc.
For more information: https://recom-power.com/en/applications/high-power-density/3dpp/3dpp.html.
Packaging Evolution: 50 years of the isolated power module
Semikron Danfoss has marked the 50th anniversary of the SEMIPACK isolated power module with the...
Smart and Safe Control Solutions for Mobile Machinery
In the rapidly evolving landscape of mobile machinery, the demand for efficient, safe, and...
The next leap in semiconductors
With companies like Intel investing in cutting-edge EUV lithography and advanced packaging...