Three ways to adjust power consumption and dissipation in your processing systems
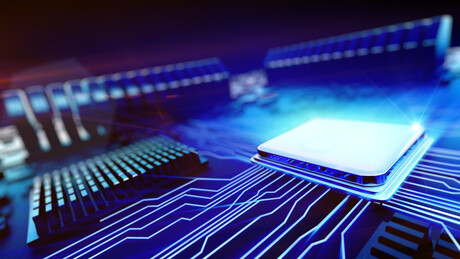
Despite the rising power efficiency of new processors, the accelerating demand for computational power often outstrips the ability to cool the systems down and/or to provide them the right amount of current. Furthermore, mechanical/thermal design usually happens late in the development cycle. Consequently, it is likely to run up against thermal limits late in the design process. Designers naturally want to optimise their systems and find acceptable trade-offs.
This paper outlines Teledyne e2v’s tailored approach proposed to system designers to adjust power consumption and dissipation in processing systems using high-reliability processors. Three different degrees of customisation are discussed and can deliver significant value to the design.
Power consumption optimisation
This consists of evaluating a population of target components, taking test data and examining the power consumption spread. Ultimately, the purpose is to select out only those devices exhibiting the best power consumption characteristics for a given application use case.
Power screening evidence suggests that for some applications when the use case is clearly defined, it is possible to operate a processor well within its operating envelope. However, this requires knowing with greater precision how the device behaves within the target use case. There is no quick answer to this, but power screening provides the detailed analysis necessary to reach a definitive understanding. In one project, Teledyne e2v demonstrated its ability to source processors with power consumption 46% lower than the worst-case standard product scenario as illustrated in Figure 1, and achieved this by combining characterisation of the customer’s application and power screening. Here, a device initially believed unsuitable for the task due to assumed excess power consumption could now be sourced and designed in with confidence.
This will not always happen and demands an understanding that power consumption within processors comprises two contributing factors; namely:
- Static or quiescent power drain — the power demanded by the IC to supply all its internal peripherals irrespective of any number crunching or code execution taking place.
- Dynamic power draw — essentially the computational power consumed. It can vary considerably in multi-core processors depending on the instantaneous computational load.
Teledyne e2v, with multiple decades of collaboration with NXP and Freescale before that, has built up an enviable knowledge of processor performance and has access to the same tools, product testers and test programs as the original manufacturer. This is the foundation that gives Teledyne e2v a credible and unique background to offer custom device power optimisation through screening and characterisation.
Processor characterisation work performed within Teledyne e2v’s manufacturing system has shown that the following characteristics are not at all unusual of current processors:
- Static power demand can vary significantly from device to device.
- Static power can be close to zero at cold, but can represent 40% or more of the total power budget at 125°C (see Figure 2).
- Dynamic power is dictated by the customer’s use case. That fortunately varies minimally from device to device, over temperature or between process lots.
Custom packaging
This consists of modifying or redesigning the existing standard product package to lower its thermal resistance from junction to board, or junction to package top:
- It can be used to reduce the junction temperature, thus lowering power consumption (assuming the same heatsink remains in place). Alternatively, it reduces the cooling system (size/weight); since the package thermal resistance (Rth) is lower, that of the heatsink can be larger.
- An alternative package can enhance vibration protection for the component and/or simplify and improve the thermal interface between the cooling system and the processor.
- To deploy a lid or not will further impact thermal performance. Depending on the application, some designers might want a lid to help integrate a heatsink more easily. Others prefer a lidless design because they can’t accept the extra thermal resistance of the lid.
Teledyne e2v has specific knowledge and experience repackaging semiconductor components. This includes but is not limited to specific package development projects, for example a package developed especially for the Teledyne e2v EV12AQ600 analog-to-digital converter. Moreover, Teledyne e2v has in-house expertise to handle the re-balling of packages to allow for solder formulation changes to suit the tin-lead alloy free needs of some space customers (eg, to protect against tin whiskers forming in space).
Another example is a feasibility study recently performed to add a lid to the NXP T1040 processor. A mechanical proposal for the optional lid was made, and revised thermal specifications were estimated. Thanks to the lid, the junction-to-board thermal resistance is expected to roughly halve to 4.66°C/W with the lid, down from 9°C/W for the standard device. In that case, the junction-to-top thermal resistance increases due to the addition of the lid, from less than 0.1°C/W to 0.85°C/W.
Extended (ie, >125°C) junction temperature
This optimisation considers the viability of operating silicon beyond conventional thermal limits of commercial, standard products. Silicon is not physically limited to operate only up to 125°C; several elevated temperature applications exist and are already served. The benefit of higher junction temperature operation is the extra thermal headroom on offer. But, as seen earlier, elevated temperatures have an implied penalty; namely, significantly raised power dissipation (see Figure 2). Where a higher junction temperature can pay off is in applications with an operating profile requiring short bursts of increased dynamic power, yet it is critical that these bursts can be handled within the thermal capacity of the design.
Thanks to in-depth product knowledge and testing experience, combined with product qualification infrastructure, Teledyne e2v can explore in detail with customers the likely operating life impact of choosing extended temperature operation. It’s an existing capability served by the company, given that Teledyne e2v already supplies NXP processors guaranteed up to 125°C — an advance over the commercial device’s 105°C limit.
Following a positive viability evaluation, Teledyne e2v can supply a custom IC specification at elevated operating junction temperature levels. This specification will be delivered in a manner that comprehends careful consideration of the following operating factors:
- Functional performance and power consumption adapted to the extended temperature required.
- Reliability, accounting for the fact that silicon components’ reliability decreases rapidly and non-linearly as temperatures rise (see Figure 3).
- Packaging ability to sustain high-temperature operation needs to be verified. Plastic epoxy packages, in particular, start to deteriorate beyond about 160°C. Repackaging with high-temperature epoxies would be a mitigation strategy here.
This paper has discussed how Teledyne e2v, building on its long-term strategic relationship with NXP, is uniquely positioned as a trusted supplier of customised processor options. Customisation is possible based on either the power architecture or ARM architecture. Outlined here were three degrees of freedom to power optimise and customise processors for harsh applications. These three options are:
- Definitive power screening for optimal use case specific power consumption.
- Alternative custom package selection for enhanced thermal handling capability.
- Raised maximum junction temperature (TJ) to support raised dynamic power demands.
Owning independent test and qualification infrastructure and having access to skilled product engineers, combined with a preferential, long-term supply agreement with NXP, gives Teledyne e2v an edge when offering specialised, high-reliability, power-optimised processor solutions for specific customer use cases in complex applications.
Packaging Evolution: 50 years of the isolated power module
Semikron Danfoss has marked the 50th anniversary of the SEMIPACK isolated power module with the...
Smart and Safe Control Solutions for Mobile Machinery
In the rapidly evolving landscape of mobile machinery, the demand for efficient, safe, and...
The next leap in semiconductors
With companies like Intel investing in cutting-edge EUV lithography and advanced packaging...