Traceability for electronics manufacturing
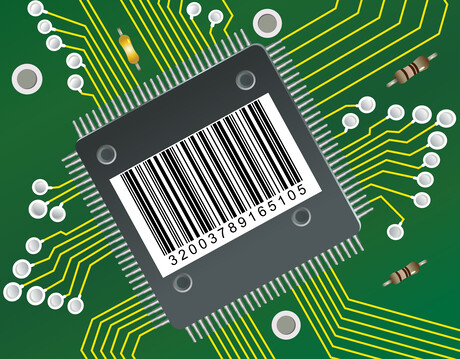
The responsibility of today’s OEM (original equipment manufacturer) and CM (contract manufacturer) is to maximise product quality with reduced costs within their manufacturing processes. This can be achieved through implementing visible automation and traceability procedures to monitor the control of materials being used during the assembly process.
With so many technological advances that are transforming the way in which we manufacture, electronic manufacturers’ main focus is to collect data in ways that allows them to track raw materials, circuit board components and assembled completed products to measure productivity and profitability. Data collection is achieved through intelligent, autonomous factory systems integrated with the internet. However, this can be a challenge for manufacturers in many industries — including aerospace, consumer electronics, medical, etc — due to the risks associated with the increasing complexity of supply chains.
Focusing on the various stages of PCB production, we look at how Industry 4.0, automation, repeatability and reproducibility can be used to improve traceability during the SMT manufacturing process.
What is traceability and why is it important?
According to the website Elhurt, traceability is the ability to trace (reconstruct the history of) the movement of components at every stage of the process chain and supply networks, together with tracking parameters which identify these components and the locations associated with their movement. Traceability solutions allow for a clear insight into each stage of the production process, thus making sure that the right material is used at the right stage of production.
The advantages of traceability within electronics manufacturing:
- Increased visibility into your operations, drives process and product improvement over time
- Detect and eliminate defects during production
- Improve quality and ensure accordance with regulations
- Minimise costs of production
- Avoid costly product recalls
- Data reporting is readily available at any time
- Positively impact customer relationships by being an overall faster more efficient company to work with
- Adhere to quality assurance standards
Implementing traceability in the SMT assembly process
With the advantages mentioned above, traceability has never been as important as in today’s electronics industry. Due to growing regulations, including warranties, returns and costs, electronic producers have a lot to gain by implementing a traceability and product recall solution within their manufacturing processes.
Fortunately, SMT suppliers are making the traceability process painless due to the various technologies offered on the market in the form of screen printers, pick-and-place machines, IT software, AOI and laser/inkjet markers. These various technologies offer speed, data storage, capacity, and connectivity. We will take a look at these systems and explore the technologies further as well as how they help manage the automation process during production.
Industry 4.0 into practice
An Industry 4.0 Smart Factory employs systems that are interconnected and able to send or receive data from the other systems in the supply chain. Smart manufacturing provides increased production control, centralised monitoring and continuous improvement. We will discuss below how various surface mount equipment can be interlinked with each other to achieve these practices.
Incoming goods
Starting the traceability process within electronics production begins with incoming goods into your facility. Ensuring that you have set yourself up with proper traceability procedures during this stage will set you up for traceability down the SMT line. As soon as reels are received, it is essential they are labelled with a unique identifier and stored where they can be easily found. The Yamaha YST15 Intelligent Storage System interlinks with mounting lines to automatically store and manage supply of surface-mount devices (SMDs). Through interlinking with a mounting line controlled by the Intelligent Factory IoT/M2M integration system, this enables centralised management of electronic component mounting processes. Surface-mount devices requiring supply can be extracted in advance from inventory at the optimal timing and supplied in batches. This advancement enables significant reductions in staff workload and prevention of production interruptions due to delays in device supply.
Barcodes of some description on your product is a necessity and they are the key to retrieving information. They hold and link all the other information associated with the production line and link it to the correct databases. Barcodes can be applied typically in three ways: through a label onto the PCB, or via laser marking or by ink jetting the required info onto the PCB. Each customer will dictate what info they want stored on each PCB; it can be as simple as a serial no or part number of the product and can be in the form of a QR code/barcode, depending on space and info to be stored in the code.
Screen printer set-up verification
There are many points to consider during screen printing, such as history, how each product was printed, when it was made, the solder paste used, process parameters and much more. The Yamaha YCP10 screen printer has the ability to monitor production runs where it can determine the type of solder paste being used, along with which stencil and squeegees were also used on the job. This is all monitored by the track-and-trace feature of the software. Engineers utilise the analytics generated from the screen printer to help make better decisions for their requirements.
Within the screen printing process, solder paste application will ensure proper board function and increase the longevity of the board and its product. The two main factors electronic manufacturers need to be able to monitor are: knowing that the solder paste being used is the right type of paste for the job, and knowing that the solder paste is not past its expiry date. Tracing the type of solder paste used for the job is made easy by using scanners on the printer and scanning the solder paste which is stored on its database.
Mounters for verification and traceability
As mentioned previously, barcoding is essential practice for every electronics manufacturer during the component placement process. By scanning barcodes on components and reels, manufacturers can capture accessible comprehensive history of how each component was placed, the reels used, the type of vendor, manufacturing batches and board mounting history by date and time. Manufacturers are also able to trace machine-related defects, which eliminates mounting errors associated with wrong part placements, allowing for no unscheduled downtime.
The Yamaha YSM20R offers an IT option — or a T (Traceability) tool option in the SW suite — which ensures that the correct part reel and feeder are installed onto the machine for that job. How this works is, the operator is requested by the software to scan each reel/feeder as part of the machine set-up and job changeover routine. This information is correlated, which ensures that no wrong parts can be loaded to the machine. Time and date stamps are initiated when jobs are set up/reels are depleted and changed. This is all recorded and stored on a database. This automation process allows manufacturers to follow standard ERP systems that utilise software containing dashboards, real-time data collected from across the assembly line to measure productivity, and profitability.
Inventory management system and data storage
Consolidating all data into one database and storing it on a server is vital for the track and traceability process. Big Data is all about collecting huge volumes of data from traditional and digital sources. These large volumes of data are generated on an ongoing basis and are a very valuable source of information, which must be analysed in real time to extract intelligence aimed at increasing efficiency or opening new business lines.
The Yamaha T:Tools traceability software and Linecontrol software from SMS International offer an endless supply of storage space where you can extract the data once you need it. With Yamaha T:Tools, the data includes test results, the movement of units through production, materials placement and more. Almost all this information is collected automatically and associated directly with each specific production unit. The tools then generate complete traceability build records. Linecontrol software can communicate with the operator at the machine in real time. The advantage is that manufacturers are able to discover valuable correlations, patterns, trends and preferences to help make informed decisions, thus improving quality, efficiency and compatibility within the business.
Laser/inkjet markers
By utilising Nutek labelling equipment throughout the entire production cycle, manufacturers can connect to every circuit board in production. The Nutek laser marking system 3 series is designed to accurately mark PCBs within a production line or can be used as a standalone cell. Every circuit board produced becomes a data generator to send information to your manufacturing execution system. Accurate tracking of raw materials and finished goods throughout production processes can increase production efficiency, especially in critical high-volume identification challenges such as aerospace, defence, electronics, automotive and medical.
The three most common methods of labelling are:
- Labelling with barcodes
- Direct labelling
- RFID technology
AOI — automated optical inspection
Once the PCBs are manufactured, an option to trace for defaults is by utilising AOI (automated optical inspection). This enables operators to ensure their PCBs have been built correctly without faults before they leave the production line. AOI captures images of the PCBs and enables them to be saved and stored on a database. The advantage of data storage is that the images of good boards and failures can be traced for future reference and recalled when needed.
Continuous improvement
Implementing a seamless, automated traceability process to your production line can be achieved and will provide you with endless benefits. Applying for ISO certifications that prove that you are a trusted supplier can help you stand out from your competition. These certifications provide assurance that your company will adhere to the most rigorous quality standards in the industry, marking it as a trusted provider.
Many manufacturers don’t maximise the traceability options on their systems and tendencies to be reactive rather than proactive seem to be the driving force behind operational change. However, technology is evolving and making traceability easier and therefore more efficient. Obtainability doesn’t have to mean a complete overhaul of processes and procedures, and a change for the better in one part of the process can gradually lead to change in others.
If you already have one of these products from Hawker Richardson and would like to know more about implementing the traceability features into your business, or you’d like to know more about any of the systems included in this article, please contact us.
References
- Yeeply Blog [online]: https://en.yeeply.com/blog/what-is-industry-4-0/
- Elhurt EMS [online]: http://en.elhurt.com/traceability-in-the-production-of-electronics/
Originally published here.
DC Microgrids: The next step in energy evolution
As we face environmental and energy challenges, DC microgrids can help pave the way for a...
Eliminate Unplanned Downtime: A Smarter Approach to Machine Diagnostics with the HYDAC HMG 4000
The HYDAC HMG 4000 portable data recorder provides a smarter, faster, and more precise approach...
Precision in Design: Specifying Large Handheld Enclosures for Industrial Electronics
When designing handheld electronics, ergonomics play a vital role; purpose-built plastic...