Selecting DC motors for small industrial-grade robots
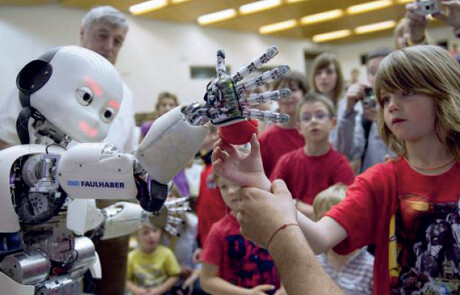
Small robotic systems
An industrial world without robotics or automation is hard to imagine. Process safety, reliability and economic efficiency are important parameters for the application of robotic systems in modern production lines.
Small robots, like their larger counterparts, are designed and manufactured to perform specific physical tasks and functions. Common to all robotics systems is the need for sensors, control electronics and motor drives for their operation.
In this article we focus on industrial-grade DC motors used in smaller robotic systems and what factors to consider when designing with such components.
Types of drives used in robots
AC motors are used widely in robot systems, especially in heavy-duty manufacturing lines; DC motors are often more suitable for end effector applications and smaller robots. This is particularly true in applications where the power source only provides low voltage and current.
There are many different types of DC motors or drives:
- Brushed DC motor (often called DC motor)
- Brushless DC motor (BLDC)
- DC gear motor
- DC servo motor
- DC stepper motor
- Direct linear drives
What is most suitable depends on the type of motion and the type of control needed for the application. For small robot applications, an industrial-grade motor should generally have the following features:
- Compact in size
- Highly dynamic
- High power density
- Short-time overload capacity
- Ability to integrate into complex motion type
- Sensor options for precise control
Motors with these features tend to be more expensive than the common ‘hobby’ style motors because they use rare earth magnets, high-efficiency bearings and other features that add to their cost.
Robot motor selection
In a robot system, when selecting a suitable motor or drive, we need to consider many different parameters for the application. Common considerations for the drive aspect are:
- Type of motion required
- Torque and speed required for the application
- Size and geometry of the drive
- Type of control required for the application
Many types of motion can be realised with the help of gearing, transmission systems and end effectors. The integration of those components can often be the most complex part of the overall system design. So, finding a suitable motor to simplify the design is often the first thing we think of when designing a robotic system. For example, a robot arm joint can be actuated with a motor and pinion couped to a ring bearing, but there are ring motors suitable for direct drive for that application.
Furthermore, it is also worth considering if a motor manufacturer can integrate components to deliver in full or in part the type of motion your design requires. For example, the following types of mechanical components can typically be integrated with a small DC motor:
- Gearheads and pinions
- Leadscrews or ball screws
- Shaft modifications
- Couplings
Most manufacturers have standard options and will consider custom options even for low-volume production.
Many designers’ initial judgment of a motor’s performance is often defined by the datasheet values for power or stall torque. These are important, but parameters such as the speed constant and torque constant provide a better idea of how much power can be developed with the available power supply.
Torque is often a difficult parameter to define because it requires some detailed understanding of the motion and load and can involve complex calculations. Many small motor manufacturers have calculation software available (sometimes on their websites) that will allow you to trial and error how a particular motor might perform.
Getting the best estimate of speed and torque is important because in each environment and over a specific period this will be the limitation for performance. Often, we must look deeper at how much temperature is being developed in operation to understand how the motor might perform in the application. Here again we may need to run calculations, but most manufacturers can assist with estimates for current, voltage and temperature — so long as the operating environment and working point are accurately defined.
Here is where the size and geometry of the drive in a small robotic system space is often critical. This is because it will often define the environment and ability to deal with heat under load.
When it comes to controlling the motors in a small robotic system typically, we require precise positioning or speed control. Therefore, the availability integrated sensors are also important.
Typically, most manufacturers integrate the following:
- Encoders (optical, magnetic, absolute)
- Control electronics
If space on the robot system is limited, an integrated controller servo combination packaged with the motor may offer value.
If there are multiple drives in the system, the ability to control or coordinate them from a single source may also be important. This is possible by either networking them to a custom electronic system or by employing an off-the-shelf multi-axis controller.
In summary, there are plenty of off-the-shelf options for industrial-grade drives suitable for a wide range of robotics applications. Designers should carefully consider their space constraints and working points for each drive in the system and explore integrated options for mechanical components and control where it is viable and cost-effective.
Erntec has been working with small DC motor solutions for many years. Talk to us for advice or selection for precision Micro-Drive solutions.
For more information, click here.
Erntec Pty Ltd
Packaging Evolution: 50 years of the isolated power module
Semikron Danfoss has marked the 50th anniversary of the SEMIPACK isolated power module with the...
Smart and Safe Control Solutions for Mobile Machinery
In the rapidly evolving landscape of mobile machinery, the demand for efficient, safe, and...
The next leap in semiconductors
With companies like Intel investing in cutting-edge EUV lithography and advanced packaging...