Maximising ROI in electronic production
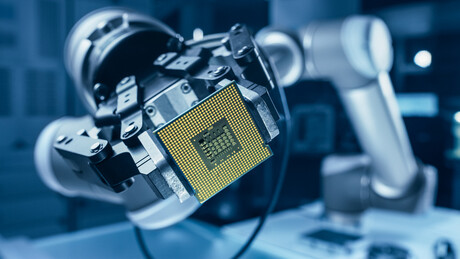
Considerations that could impact ROI dramatically
When considering your next investment in electronic production, whether it’s a new oven, pick and place mounter, printer, or a whole new line, there are quite a few considerations that could affect your return on investment (ROI). You may have already thought of most of them, but its only too easy to get caught into comparing system specifications, and yet other important factors such as spare parts availability might only come to the forefront in a crisis, costing you a considerable amount of downtime.
There are quite a few considerations you should take when looking to maximise ROI. However, to make this easier, we have split the information into three sections: how choosing, operating and maintaining your system/s can impact ROI.
How choosing the right system can impact ROI
Most buyers will do a fair amount of due diligence and list and compare specifications, packages and prices. If you are looking for a single system to integrate with an existing line, then it is essential integration is considered from both a hardware and software perspective. For example, if you are already utilising a Yamaha Surface Mounter such as the YSM20R, and you are looking to incorporate storage solutions, then choosing a YST15 Intelligent Storage System ensures both systems will integrate seamlessly. This is achieved through interlinking with a mounting line, controlled by the Intelligent Factory IoT/M2M integration system (or Specialised Machine Software SMS), enabling centralised management of the electronic component mounting processes.
Not only is the software crucial for driving full automation within the line, but the impact on setting up your mounter can save you hours. For example, the Yamaha YSM20R allows engineers to setup the feeder carts offline. It negates the need to cease operation, therefore downtime is minimised and production maximised affecting productivity and ROI. What is more, the YSM20R provides a Non-stop Feeder exchange that allows operators to change individual feeders / feeder carts while the system is still in operation.
This is why it is essential you determine if you need to configure your machine with feeder exchange carts, rather than fixed feeder banks, from the outset. Feeder exchange carts allow for much faster job changeovers with minimal machine downtime. It is also worth noting that it’s not feasible to convert the machine once it has been delivered.
Integrating other hardware such as conveyors can utilise a ‘Follow Me’ function which allows integration and communication with neighbouring SMT machines, both physically and through software. Ensuring marginal gains are utilised by the optimisation of synchronised SMT systems can lead to a surprising advantage in yield and therefore ROI.
Most businesses looking to invest in capital equipment such as an SMT line, would usually compare lots of elements including functionality and features versus cost and output. However, even once you have documented all of the possibilities and you think you have made a decision, it is worth speaking to other businesses that have invested in the same system/s. This will ensure that the systems you have chosen can actually fulfil their specifications. Some placement systems might boast placement size of 0603, but ensuring this can be done at the speed stated, and without the requirement for rework or wastage is advised. For example: one of our customers ran the Yamaha YSM20 and a competitor’s systems and found they had a lot of rework on the 0603 placements using the competitor’s system. Not only did they find a 25% increase in accuracy with the Yamaha, they also found it could place the 0603s at twice the speed. This also suggests that you don’t always have to compromise on speed to get excellent accuracy.
Having the capability to maximise yield is important, especially if you are a subcontractor and require the flexibility in your line to step up or down. However, if you are an OEM and your requirements are consistent, it is worth considering that some SMT systems can run significantly richer than others i.e. ovens tend to utilise most power consumption in the SMT line and ensuring you only invest in what you need will minimise energy consumption, which accumulatively can have a significant effect on ROI.
For example, Heller’s latest generation of convection ovens have been designed to reduce electricity consumption by up to 40%. This not only increases your ROI but affects your triple bottom line with benefits to the environment too.
However, if you are in the business of manufacturing a variety of boards, you need to consider if you need a centre board support in your reflow oven. If you are likely to be producing wide or heavy PCB’s it would be best to purchase an oven with centre board support. Whilst it is possible to retrofit centre board support it is a very time consuming task and at a greater cost.
Before signing on the dotted line, it is advisable that you order extra parts i.e. order spare feeders if you are investing in a mounter. Nobody wants to think of requiring new parts when they are ordering a new system, but it’s a fact that parts such as nozzles and filters will need replacing as you use your system, and ordering spares at the same time as the new mounter will save costs associated with freight on a separate order.
Not only will ordering spares (nozzles and filters) upfront save the freight costs, it’ll also minimise unnecessary downtime.
Achieving operational excellence with a continual improvement strategy can increase ROI as well as improving quality.
Other environmental concerns which can also affect your return, is your waste. High value boards can be reworked, but incorporating an automated optical inspection (AOI) system into your line, could increase your ROI. Scanning your boards in ‘real-time’ and stopping production if it finds a fault, could save you from running a full batch, only to find a component has been mounted incorrectly. Implementing an AOI process and system into your line is essential.
As long as there is a human aspect to your production, there is always a chance of human-error. Whether it’s loading a component the wrong way into the feeder, or in some cases it can be at the end of production i.e. applying conformal coatings. Ensuring your boards are not spoilt on the last leg is essential. In-line systems such as the PVA solution can provide repeatability and reproducibility to the process, eradicating human-error, thus preventing unnecessary waste or rework.
Even once you have minimised the human-error variables from your line, there will always be something that crops up unexpectedly. With higher value boards it is worth thinking about implementing traceability through barcoding or laser marking. This is especially important if you have no space for an AOI.
The traceability function will allow you to track back easily to identify faults. This can save a lot of time and ultimately affect ROI because it’ll minimise downtime.
Similarly, you may find that some of the more critical issues with the boards are not with the mounter, but with the printing process and / or the solder paste. Utilising an SPI - Solder Paste Inspection system could prevent any boards from being processed through to the mounter, if there were imperfections with viscosity or alignment inaccuracies with the paste during printing. If the board were to process through the mounter with the solder or printer faults going undetected, it’d end up requiring more time to correct / rework, and more money off the bottom line.
Maintaining your system is essential to ensure it continues performing to its greatest accuracy and efficiency.
All machines need to be maintained regularly. It is false economy to not maintain machines, they will eventually end up in poor condition and will be less reliable than a well maintained machine.
With the requirement for regular maintenance in mind, ensure you know how long it’ll take to book an engineer for maintenance. It is quite common in Australasia to wait a number of weeks to book an engineer to come to site. With this in mind, you should ask your supplier what lead time is required, because if something were to happen which would stop the SMT line from operating, a couple of weeks of downtime is unacceptable. Even if you could get an engineer to site within days and you are lucky enough to experience ‘right first time’ trouble shooting, you may still have to wait weeks for parts. So don’t be left high and dry, ask the right questions for long term operational excellence.
How long does it typically take to get an engineer on site?
How experienced are your engineers with this make and model?
Do you stock spare parts or do they need to shipped from offshore facilities?
New Tech Tuesdays: Big Data, Bigger Insights: The Power of Datafication
Join Rudy Ramos for a weekly look at all things interesting, new, and noteworthy for design...
What's driving the future of Power over Ethernet?
PoE technology has come a long way since 2003. Take a look at some of the trends and developments...
Arduino — communication using the Ethernet network
Check how to use the Arduino platform in your IoT and IIoT network.