Sensors for bridge monitoring
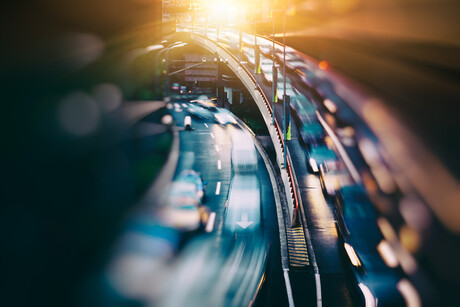
The global population is growing — the United Nations estimates the count to hit 8.5 billion in 2030 — which increases the need for reliable infrastructure to house and transport citizens worldwide.
Bridges of all kinds are part of this essential infrastructure, helping goods and people to move through previously inaccessible corridors. Bridge maintenance and repair to stay on top of unfolding problems and fix them before severe damage occurs are complex processes that a variety of electronic sensors help facilitate.
Bridges and structural health monitoring
According to the 2021 report card on America’s Infrastructure from the American Society of Civil Engineers, “There are more than 617,000 bridges across the United States. Currently, 42% of all bridges are at least 50 years old, and 46,154, or 7.5% of the nation’s bridges, are considered structurally deficient, meaning they are in ‘poor’ condition.” In the absence of a complete overhaul of these structures, we need a network of sensors that can monitor the bridges, especially since, according to the report, “178 million trips are taken across these structurally deficient bridges every day”.
The monitoring of bridges has undergone its own kind of evolution over many years. National Bridge Inspection Standards in the United States mandate a specific frequency of visual inspections. When periodic visual reviews, say, at an interval of six months, reveal potential problems, maintenance professionals increase the frequency of inspections, adding more sensors and advanced technical solutions into the loop.
The thesis of ongoing structural health monitoring (SHM) is that by the time periodic visual inspections find any problems, it might already be too late to forestall significant damage. SHM keeps a pulse on the varying conditions that might not be readily visible to the naked eye. SHM promises that it can catch problems early and avoid expensive repairs, road closures, and more. The cost of SHM is also not insignificant but is favoured as an approach that not only keeps business humming but also potentially saves lives.
To keep bridges going, engineers field data from two fronts: repairs and ongoing maintenance. Sensors play a role in each of these categories. Keeping bridges safe requires a frequent ongoing analysis combined with detection and troubleshooting if something does go wrong. In essence, bridge analysis is for the prevention of problems and troubleshooting when failures occur. For prevention, professionals can choose periodically scheduled visits, including visual inspection and measured data. Alternatively, periodic remote monitoring is also a possibility. Advanced computing capabilities and artificial intelligence that feeds on data from sensors have accelerated the move toward continuous monitoring.
Parameters to measure
To get a clear picture of bridge health, industry professionals need to measure a few different parameters. These include:
- External loading such as those contributed by wind and traffic. Measuring the wind velocity and direction is essential to determine cable vibration — to prevent cables from failing and snapping prematurely. Structural twisting of the bridge can also occur due to wind effects. Wind adds to loading problems, as does traffic. Often traffic tonnage will need to be monitored, and large trucks diverted if needed.
- Structural effects over time like strain, displacement of structural units. Measuring strain tells how much stress the bridge is under, which can signal imminent failure. Measuring girder displacement, for example, gives professionals an indication of material stiffness and flexibility.
- Environmental effects like temperature, wind, humidity, rain and other precipitation as they affect bridge conditions in the near and long term. Rising temperatures affect a range of relevant parameters, especially over time. An extreme range of temperatures is also problematic as it can gradually deteriorate bridge materials.
-
The effect of environmental conditions, like corrosion, which also leads to bridge parts failure. Steel cables have kept construction costs low, but corrosion is an ongoing challenge that can lead to failure and needs monitoring.
Cracking, tilting of decks and panels, water levels around bridges that might affect the foundation's strength on which bridges rest, settlement, vibration, and fatigue, are all critical considerations. The exact combination of parameters that engineers need to measure depends on the specific geographies of the area in which the bridge is situated. In rainy regions, for example, we might need more frequent monitoring of rain-driven corrosion, while bridges over rivers might need to pay attention to riverbed scouring that accompanies erosion.
Sensors to use
The long list of potential sensors to use for measuring these different parameters might include:
- Vibration-based monitors like accelerometers. These measure the way the bridge is tilting along all three axes. Tilt can be induced by a wide range of persistent environmental conditions, including wind and traffic. Taken consistently over a period of time, vibration-based monitoring can paint a clear picture of the overall structural integrity of the bridge. Accelerometers are also extremely effective at gauging the effect of a dramatic change in operating conditions — for example, an earthquake — on bridge function. An accelerometer sensor works by measuring the vibration from the element over which it is placed and then converting that signal into measurable electrical output.
- Strain gauges for strain-based monitoring of steel and reinforced concrete and other materials on bridges. A common type of strain gauge has a metal foil pattern that, when subject to strain, deforms and changes its electrical resistance. Measuring this change gives users a measurement of the stress on the structures.
- Tiltmeters are used to measure how much a bridge has moved beyond its initial designed and constructed mode. A tiltmeter functions much like a spirit level with a bubble that indicates how much off-center the element is.
- Fiber optic sensors measure a range of parameters like temperature, pressure and humidity. The transmission of light and its subsequent behaviour as it passes through materials is the foundation for measuring the parameters listed. The thesis is that different materials have different ways of bending or otherwise interacting with light.
- Load sensors for checking weight on bridges.
- Crackmeters and jointmeters to measure movements of cracks and at joints. Crackmeters have a sliding element, so when the sensor is situated on top of the crack, the movement of the sliding element reflects the growth of the crack.
The move to IoT and cloud-based solutions
Bridge engineering is moving toward making the routine maintenance aspects a more rigorous technology-driven solution. The growth of artificial intelligence — data over a period of time can inform us about potential breakdowns or find patterns of abnormal behaviour — is leading to a revised approach toward sensor data collection and processing.
Contemporary bridge monitoring solutions use the Internet of Things (IoT) technology to frequently sample data and relay them to a data-processing model in the cloud. Bridge engineering borrows a page from manufacturing, creating a digital twin from all the data inputs to understand how the different parameters affect each other and how modifying one could affect the rest. Sensors often feed on solar energy or might use batteries that only wake up periodically when needed, thereby conserving energy. In new construction, sensors can also be embedded in bridge materials, forming a part of the monitoring solution from the start.
The cloud-based, digital twin, sensor-driven method of bridge monitoring is gaining traction in the industry. In Norway, for example, a digital twin version of bridge operations helped avert a major disaster when parts of a vital Stavå bridge between Oslo and Trondheim were observed to be actually shaking. The real-time data helped professional teams zero in on solutions faster.
Real-time monitoring in this fashion is increasingly proving to be more effective than the traditional periodic sampling method, especially since inspections are mandated only every few years in many cases. Even without a digital twin, simply recording pattern behaviour of various interrelated parameters and studying them over time helps detect problems proactively. In manufacturing, Industry 4.0 uses IoT-embedded sensors to deliver predictive maintenance. Bridge engineering can achieve similar results with a network of sensors all instrumented together and providing data that can feed into artificial intelligence or machine learning models.
One of the many advantages of such an IoT-based continuous sensor solution is that problems are spotted early and can be fixed at less expense and disruption than if they lead to breakdowns and potential loss of lives. The cost savings, too, is appealing to governments on a tight budget. Another advantage is that continuous monitoring can be set up to function remotely, so teams of experts need not be dispatched, adding to maintenance and repair costs. Managing regulatory compliance and extending the life of assets are additional advantages.
Conclusion
Where bridge monitoring used to be a periodic and occasional process, it can now be dynamic and ongoing with sensors connected to the cloud and delivering forecasts about conditions in real-time.
As infrastructure maintenance is a high-priority task for many state and local governments, they are working on using the most efficient solutions to get the job done right. Advanced sensors that measure various crucial parameters will continue to be an essential part of a technology-driven solution, both for ongoing monitoring and repairs as needed.
In the future, expect bridge engineering to continue to include advanced technologies such as machine learning and artificial intelligence as it increasingly embraces cloud-based IoT-driven monitoring solutions. Sustainability pressure and infrastructure budgets are putting a squeeze on governments. But technology can provide efficient and reliable solutions.
IO-Link solutions for the fluid power industry
The IO-Link pressure sensors and transmitters from HYDAC allows for three types of data to be...
People Counting Technology: Integrating ADI EagleEye Adds Intelligence to Your Solutions
ADI EagleEye™ enables a complete end-to-end, edge-based hardware and software technology...
Sensor applications for driving efficiency in electronics production
The laser triangulation sensor has a compact design and is capable of adapting to rapidly...