Root cause analysis to enhance switch display development
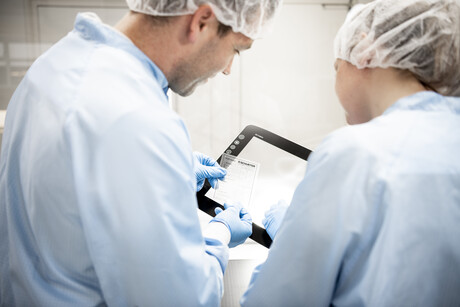
New customer projects are not always easy to realise — customised, optimised processes can help and lead to even greater success in series production. Human machine interface (HMI) solutions can be demanding; the specifications for the input system for such projects are challenging. Therefore, it is vital to work with an experienced manufacturer to optimally realise these high-end solutions.
For a customer from the automotive high-end vehicles sector, SCHURTER started with the series production of a ‘switch display’ as a component of the central control console with independent functions. In this specially designed input system, the display integrated into the housing shows the symbol of the selected function.
For each project, various specifications can be agreed upon with the customer. Rejects and error rates that are found within a defined tolerance are also part of this. A qualitative 100% realisation does not exist in reality due to various parameters, but is still strived for. In this case, the formation of bubbles between the display and the housing posed the greatest challenge due to the complexity of this customised HMI solution.
SCHURTER strives to manage, monitor and improve excellent processes. Its management systems and certifications according to ISO 9001, ISO 14001, ISO 13485 and ISO 45001 are regularly monitored and practised. As a result, it is constantly improving products and processes in order to offer the best possible solution.
In this project, a working group for root cause analysis and process improvement was formed. The starting point was the root cause analysis according to Ishikawa and other models. This identified several potential causes for bubble formation, including residual traces of powder in laser processes, reduced adhesive properties of display/housing, dust inclusions, and fixture and process parameters.
With the help of this root cause research and the set-up of various test series, methods and measures were systematically developed for improvement within a short period of time. Nothing was left out, with all influencing factors such as machine, operator, environment, material, method and measurement considered. The entire process chain and supply chain were also thoroughly re-examined.
Since SCHURTER has an in-house qualification laboratory with a range of test equipment, various sources of error could be identified and eliminated. The in-house engineering team in the area of process and mechanical engineering was also able to contribute to the implementation of the optimisation measures.
To improve adhesion, the individual components were specially pre-treated. Dust inclusions were also minimised to a regulated level by optimising production in the cleanroom, including personnel and secure premises. The bonding process was also optimised by adapting the fixtures used.
For such fine optimisations, the extensive knowledge of SCHURTER’s engineers from the engineering and quality departments was crucial, as it meant that SCHURTER had the ability and knowledge in-house. This allowed it to achieve such process and quality improvements. The company also looked beyond, to the entire supply chain, which enabled it to initiate an improvement measure with the supplier of the housing. In cooperation with the supplier, the laser process there was optimised, this reducing the traces of powder.
At SCHURTER, the quality of products and services is considered a key factor for success. Expert knowledge is vital to realise such challenging projects. After making these small adjustments and implementing various measures, the error rate for bubble formation was reduced by ~70%. This illustrates that SCHURTER’s high standards of quality, products and services offer great potential for improvement. The use of in-house specialists and sharing of ideas means a profitable analysis and implementation of measures is possible.
This also shows that high quality standards and the achievement of 100% solutions have great potential. SCHURTER is constantly improving and optimising, in order to offer the best possible solution. In a team, both internally among the SCHURTER specialists but also with direct exchange with the customer and suppliers, optimal solutions can be created which lead to success.
Phone: 0011 65 6291 2111
EXAIR ATEX cabinet cooler systems
The ATEX Cabinet Cooler Systems are designed to keep electrical enclosures cool in hazardous ATEX...
FUJI Smart Factory Platform NXTR A model
The NXTR A model pick and place machine is designed to enhance productivity, maintain...
Epoxy Technology Hybrid 353ND
The Epoxy Technology Hybrid 353ND is suitable for bonding, sealing and coating applications in...